;
;
;
Next Article
New mayor leads tide of change
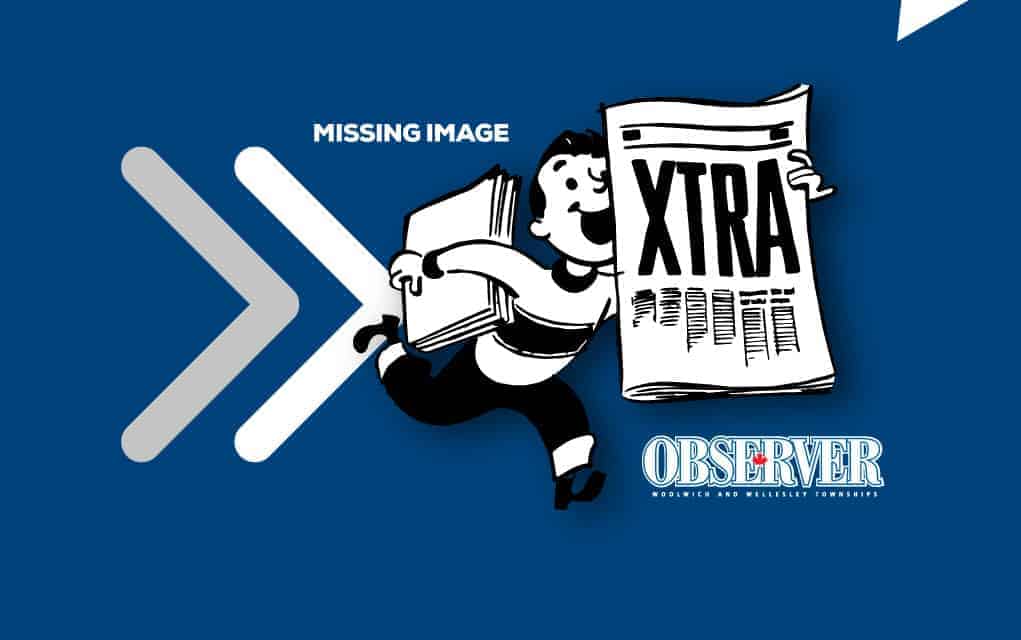
Sculptor Timothy Schmalz has spent the past 20 years creating artwork all around the world, from his studios in Mexico City and Thailand, to unveiling sculptures and statues up to 25-feet tall throughout North America and Europe. Compared to his globe-trotting exploits, however, his latest creation
Last updated on May 04, 23
Posted on Oct 29, 10
3 min read